Two-photon polymerization (TPP) has become a key technology in the field of 3D nanofabrication, thanks to its high resolution—down to the sub-100-nanometer scale. However, traditional TPP printing systems typically rely on point-by-point serial scanning, which severely limits throughput and poses significant challenges for industrial adoption.
In contrast, Femtosecond Projection Printing (FP)—a method based on spatiotemporal focusing of femtosecond lasers—offers a breakthrough by significantly enhancing the speed of 3D nanoprinting. This innovation enables rapid and continuous fabrication, paving the way for industrial-scale applications.
This article takes a deep dive into the principles behind spatiotemporal focusing with femtosecond lasers, explaining how this approach accelerates the 3D nanoprinting process and unveiling the core technologies that make it possible.
Introduction to Femtosecond Lasers
To understand Spatiotemporal Focusing technology, it is essential to first gain a basic understanding of femtosecond lasers.
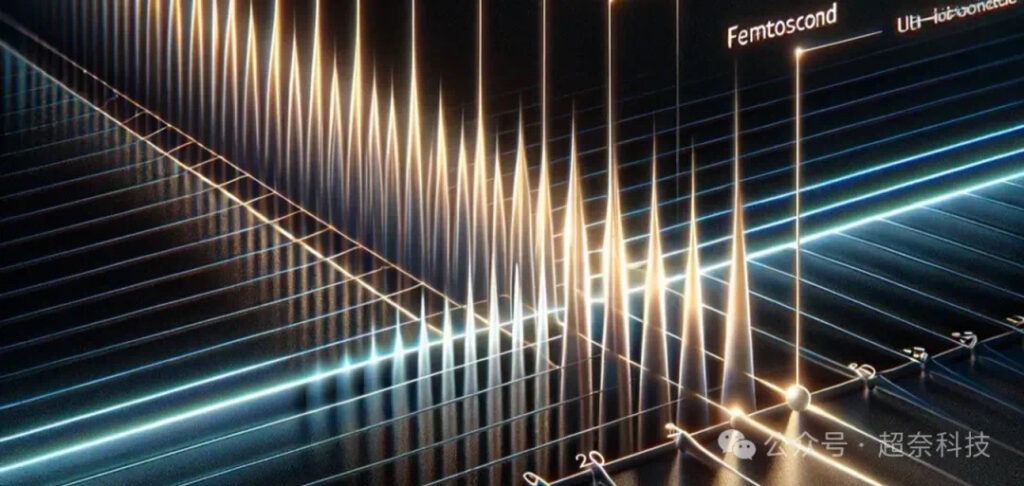
What is a Femtosecond Laser?
A femtosecond laser generates a sequence of light pulses, each with an extremely short pulse duration on the order of femtoseconds (~10⁻¹⁵ seconds). Each individual pulse in the sequence lasts for an ultra-brief moment.
In the time domain, due to the ultrashort pulse width, a femtosecond laser delivers extremely high peak power under the same pulse energy, following the relation P=E/tP = E / tP=E/t. This high peak power gives rise to unique physical and chemical interactions between the laser and materials. Moreover, because of the brief pulse duration, femtosecond lasers can process materials with minimal thermal effects, avoiding the accumulation of heat that might otherwise compromise printing quality. This is particularly valuable, as most materials exhibit thermal relaxation times on the order of nanoseconds (10⁻⁹ s) to picoseconds (10⁻¹² s). These properties make femtosecond lasers highly suitable for precision micro/nanofabrication.
In the frequency domain, femtosecond lasers exhibit broad spectral bandwidth. This results from the Fourier transform relationship between the time and frequency domains—shorter pulse durations correspond to wider spectral bandwidths. However, a broad spectrum alone does not guarantee ultrashort pulses; complex techniques, such as mode-locking, are also required to generate stable femtosecond pulses. Due to space limitations, we will not delve into these methods here.
What’s essential for understanding temporal focusing, which will be introduced later, is this key principle:
All spectral components of a femtosecond pulse must be spatially overlapped to form a true ultrashort pulse.

Introduction to Multiphoton Lithography
Multiphoton lithography (also known as laser direct writing) is a fabrication technique similar to conventional photolithography, where light of a specific wavelength is used to expose either positive or negative photoresist to create micro/nanoscale structures. Unlike traditional photolithography, however, this method does not require a photomask, significantly enhancing its efficiency for rapid prototyping in the micro/nano fabrication domain. It also enables the printing of complex three-dimensional structures with sub-micron resolution.
What is Two-Photon Polymerization (TPP)?
Two-photon polymerization is a specialized branch of multiphoton lithography. Its fundamental physical mechanism is two-photon absorption (TPA), a nonlinear optical process that occurs during the interaction between femtosecond laser pulses and photosensitive resins. Only when the laser intensity exceeds the polymerization threshold of the resin does polymerization occur—localized precisely near the focal point—transforming the liquid resin into a solid structure (as illustrated below).
Through subsequent development steps, the unexposed liquid resin is removed, leaving behind the desired 3D micro/nano structure. Today, TPP technology has been widely adopted for fabricating a broad range of 3D microstructures. Common applications include integrated optics (such as waveguides, photonic crystals, and metamaterials), microfluidic devices, optical data storage chips, and even quantum photonic chips, among many other advanced use cases [5–10].
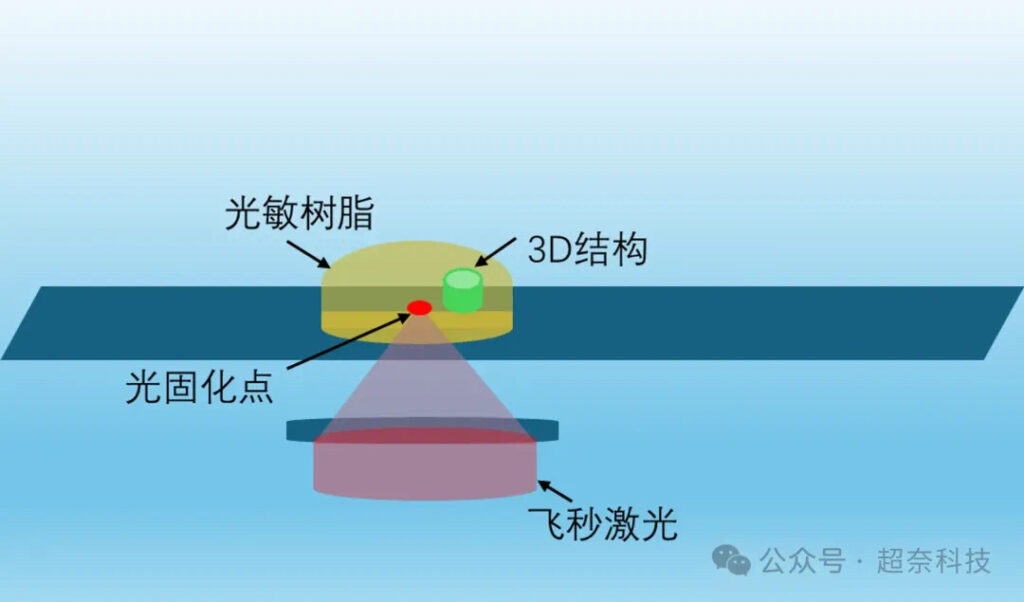
Overview of Spatiotemporal Focusing
Spatiotemporal focusing of femtosecond lasers was independently proposed in 2005 by scientists Chris Xu [1] and Yaron Silberberg [2]. The technique was originally developed to address the speed limitations of two-photon fluorescence microscopy. By transforming the traditional point-by-point excitation method—commonly used for biological samples—into a plane-based excitation approach, this innovation enabled significantly faster volumetric imaging.
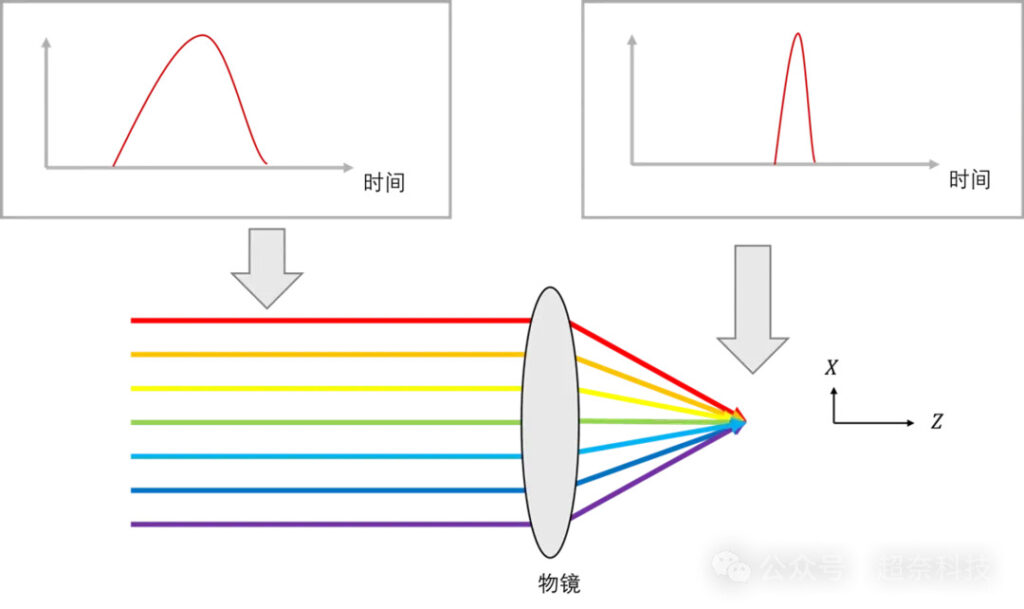
As illustrated in the figure above, the basic principle of spatiotemporal focusing is similar to conventional spatial focusing in that light is focused through an objective lens. However, unlike traditional approaches where all spectral components remain overlapped in space, spatiotemporal focusing intentionally introduces spectral dispersion.
Initially, the femtosecond laser pulse is spatially dispersed using a dispersive element (such as a diffraction grating or prism), meaning that the conditions for generating a femtosecond pulse are temporarily unmet. The spectral components are then refocused spatially through the objective lens. At the back focal plane, all frequency components arrive simultaneously and without chirp, thereby satisfying the condition for femtosecond pulse formation. This setup enables the reconstruction of the shortest pulse duration precisely at the focal plane.
The figure below clearly illustrates the key advantage of temporal focusing over purely spatial focusing: large-area excitation.
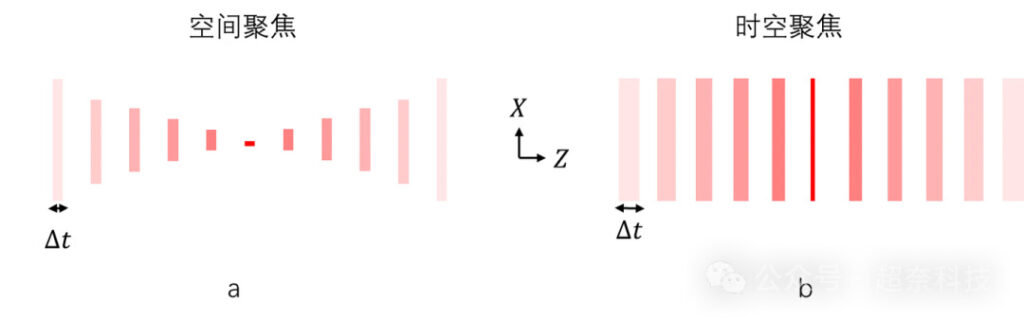
Figure a illustrates the traditional two-photon excitation technique. In this method, an ultrashort laser pulse is spatially focused to a single point, generating a high peak intensity at the focal spot. However, as the pulse travels through certain media (such as photoresist), its temporal duration remains nearly unchanged. If the intensity is sufficiently high, polymerization may occur both before and after the focus, potentially reducing axial precision.
In contrast, Figure b demonstrates how temporal focusing influences the pulse width (Δt) and illumination area. Firstly, the illuminated spot size near the focal plane is several orders of magnitude larger than that of spatial focusing, enabling planar (wide-area) excitation. Secondly, as the pulse propagates through the sample, its temporal width becomes broadened—only at the focal plane does the pulse compress back to its minimum duration and reach peak intensity. Away from the focus, the stretched pulses fail to reach the threshold needed for two-photon absorption, greatly improving axial resolution and reducing unwanted polymerization.
Technical Implementation
Initially, temporal focusing was achieved by using a diffraction grating to spatially disperse the spectrum of femtosecond laser pulses. This was followed by a 4-f optical system that conjugated the grating to the back focal plane of the objective lens, effectively projecting the grating onto the sample surface. However, in this original setup, the grating was static and unable to support dynamic pattern switching. As a result, the application of this method was limited to two-photon imaging, enabling only rapid planar excitation for imaging purposes.
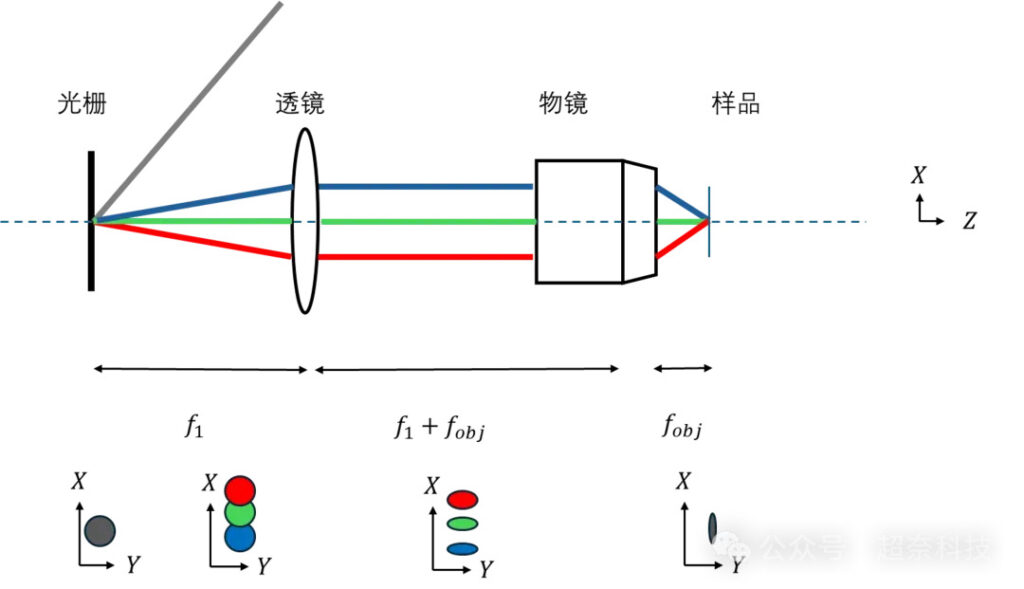
Subsequent Development
The research team led by Professor Shiqi Chen at The Chinese University of Hong Kong made significant advancements in this area by integrating a Digital Micromirror Device (DMD) into the temporal focusing system. As a type of two-dimensional diffractive optical element, the DMD naturally introduces spectral dispersion to femtosecond laser light, similar to a conventional grating.
More importantly, the DMD serves as a dynamically programmable element, enabling diverse and flexible pattern projection. This breakthrough transformed temporal focusing from a static imaging method into a dynamic projection printing system. The basic optical configuration of this system is illustrated in the schematic below.
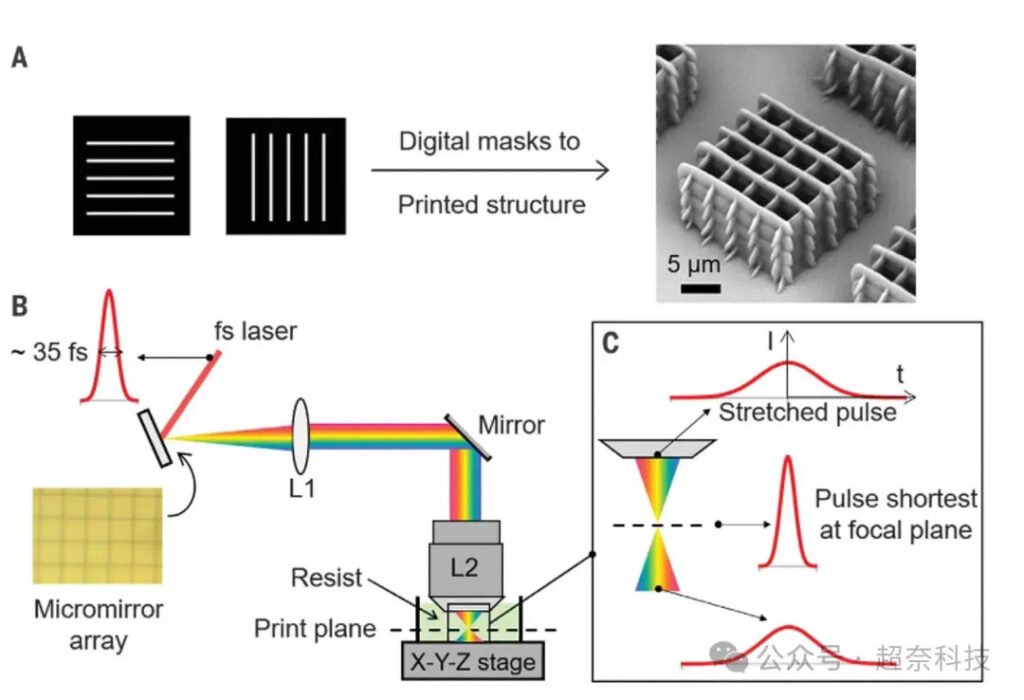
Challenges and Breakthroughs in System Implementation
During the development of the new system, Professor Shiqi Chen’s team faced two major challenges: femtosecond laser stability and strict environmental control. The operation of high-energy lasers requires precisely maintained environmental conditions—even the slightest deviation or instability can result in critical errors during the printing process, potentially leading to entire print failures.
To address this, the team employed a range of high-precision equipment, including ultra-precise displacement stages, environmentally controlled laboratories, and standardized post-processing procedures, enabling the successful execution of ultra-high-resolution printing.
Another significant challenge was dispersion control of femtosecond lasers. Poor dispersion management directly compromises the achievable resolution. To overcome this, the team conducted extensive experiments and simulations to fine-tune the system and optimize the printing process based on the principles of temporal focusing.
This innovative advancement was published in Science in 2019, earning widespread recognition and multiple awards.
The following images showcase some of the latest experimental results produced using this system. They demonstrate that print speed can be significantly improved without sacrificing resolution, offering strong competitive advantages over existing commercial 3D nanoprinting systems.
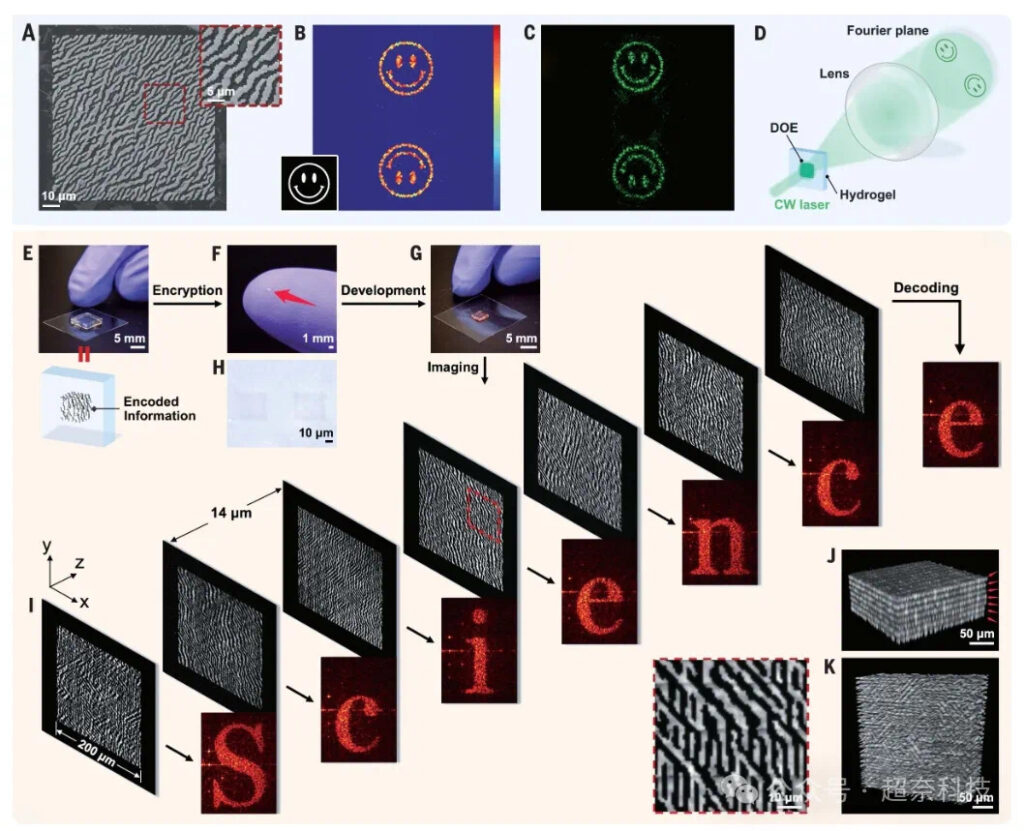
Conclusion
Originating from the field of two-photon fluorescence imaging, spatiotemporal focusing of femtosecond lasers has gradually expanded into 3D nanofabrication and continues to evolve through ongoing research and innovation. Compared to traditional point-by-point excitation methods, this technology enables wide-area (planar) excitation, significantly enhancing processing efficiency.
Under the continuous refinement and innovation of Professor Shiqi Chen’s team, the technique now supports customizable, high-speed 3D structure fabrication. Its broad applicability, combined with the ability to dramatically increase printing speed without compromising resolution, positions this method as a highly promising solution for the future of advanced nanomanufacturing.
Reference material
[1] Zhu, Guanghao, et al. “Simultaneous spatial and temporal focusing of femtosecond pulses.” Optics express 13.6 (2005): 2153-2159.
[2] Oron, Dan, Eran Tal, and Yaron Silberberg. “Scanningless depth-resolved microscopy.” Optics express 13.5 (2005): 1468-1476.
[3] S.K. Saha, D. Wang, V.H. Nguyen, Y. Chang, J.S. Oakdale, S. Chen, “Scalable Submicrometer Additive Manufacturing,” Science, Vol. 366, No. 6461, pp. 105-109, 2019.
[4] Sugioka K, Cheng Y. Ultrafast lasers—reliable tools for advanced materials processing[J]. Light: Science & Applications, 2014, 3(4): e149-e149.
[5] Gansel, Justyna K., et al. “Gold helix photonic metamaterial as broadband circular polarizer.” science 325.5947 (2009): 1513-1515.
[6] Watanabe, Wataru, et al. “Wavelength division with three-dimensional couplers fabricated by filamentation of femtosecond laser pulses.” Optics letters 28.24 (2003): 2491-2493.
[7] Skryabin, N. N., et al. “Two-qubit quantum photonic processor manufactured by femtosecond laser writing.” Applied Physics Letters 122.12 (2023).
[8] Piacentini, Simone, et al. “Advanced photonic and optofluidic devices fabricated in glass via femtosecond laser micromachining.” Optical Materials Express 12.10 (2022): 3930-3945.
[9] Lyu W, An J, Lin Y, et al. Fabrication and applications of heterostructure materials for broadband ultrafast photonics[J]. Advanced Optical Materials, 2023, 11(12): 2300124.
[10] Liu H, Lin W, Hong M. Hybrid laser precision engineering of transparent hard materials: challenges, solutions and applications[J]. Light: Science & Applications, 2021, 10(1): 162.
[11] Han, Fei, et al. “Three-dimensional nanofabrication via ultrafast laser patterning and kinetically regulated material assembly.” Science 378.6626 (2022): 1325-1331.